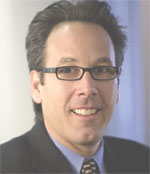
The basic operation of an optical profiler is to split a beam of light exiting a single source into two separate beams and then recombine them to create the bright and dark 'fringes' that make up an interferogram. Like the lines on a topographic map, these fringes represent the topography of the observed object. Optical profiling, also known as white light interferometry, is thus a non-contact technique for determining small-scale surface texture and shape. It combines high speed, a wide measurement area, large vertical range, and subnanometer vertical resolution.
This unique set of strengths supports a variety of applications in R&D, product and process development, manufacturing, and quality control – from characterising auto clutch wear and free-form optics to analysing semiconductor defects and electrostatic damage to food packaging. One particularly rewarding area has been its use as a fundamental metrology tool for MEMS development and production.
MEMS devices are revolutionising nearly every product category. Current industry projections by In-Stat and others estimate that MEMS shipments will grow 20 per cent per year for the next four to five years, to as many as six billion units by 2009. With funding increasing by 40 to 50 per cent per year for MEMS companies, this maturing technology will continue to penetrate other markets and will be combined increasingly with other technologies.
The microfabrication of MEMS devices allow unprecedented levels of functionality to be placed on small silicon chips. Obviously, such complexity and the demand for absolute repeatability make quality control of crucial importance in providing a successful and affordable end product. For this reason, optical profiling has had great play in the MEMS markets, and much effort has been expended in advancing metrology methods to better suit both mainline and niche MEMS products.
Until recently, interferometric measurements were confined too early in the MEMS manufacturing process. These static, unpackaged measurements have been instrumental in verifying and controlling MEMS etch and deposition processes, yet have been largely unable to fully characterise how a device will react under actual working conditions. The continuing evolution and widespread use of MEMS created a very large need for characterising microdevices in motion, as they actuate, as well as within their glass, plastic, or sapphire packaging. Since 50 to 80 per cent of the total cost of MEMS production comes from final packaging and test, the dynamic MEMS market is an area within which optical profiler companies desperately want to compete.
Resulting profiling innovations utilised other optical technologies to help MEMS manufacturers lower these costs by measuring motion at the wafer level with a profiler incorporating strobing capability. The addition of strobe illumination allowed the measurements to be timed to the frequency of the MEMS movement, effectively freezing the motion and providing a series of measurements over the entire functional range of the microdevice. A number of commercial instruments were developed that allowed MEMS manufacturers to study released, die-level criteria in unlidded, packaged devices for the first time. Crucial corrections could thus be performed before final packaging, at lower cost, giving competitive edge in the MEMS manufacturing marketplace, as well as increased value to the end consumer.
The newest innovation decreases manufacturing costs even further and enables crucial, final verification in lidded, packaged devices. As with the dynamic MEMS characterisation, profiling through transmissive media combined profiling with other optical technology. Objectives with long working distances were fitted into a reworked optical profiler light path, and fibre-optic laser shape illumination was added to control dispersion aberrations. The longer working distance and shaped illumination allow high-magnification interferometry of MEMS devices through varying thicknesses of packaging for the first time. Now, end consumers can be provided with more reliable devices without significant cost increase on the part of the manufacturers.
A significant aspect to overcoming the challenges in developing such new technology is making the resulting solutions simple, affordable, and flexible enough to warrant commercial viability. As in all R&D endeavors there is inherent risk, but if you can put a resilient, adaptable team in place, and keep a watchful eye to the future, it is possible to gracefully shift from profit cusp to profit cusp. The very technologies you create to feed the evolution of applications in one field will spawn possibilities in other areas. Optical profiler manufacturers are already finding ways to fit the technology created for MEMS to emerging, high-growth areas such as RF and microfluidics applications. This is the true synergistic role of scientific technology. And though there are winners and losers in the marketplace competition it is important to remember that, if we do our jobs correctly, these technologies will build upon each other and improve our world in unforeseen ways.
Please send any comments/feedback to the editor at editor.electro@europascience.com