Beam shaping technologies open up new possibilities and processing options for controlling heat input during laser materials processing. For high-power applications, beam shaping is usually done through either beam oscillation or by manipulating the spatial intensity distribution of the beam in one layer to create, for example, several laser spots, tophat profiles or donut profiles.
Refractive optics for high-power laser applications
Refractive beam shaping, which uses either mirrors or lenses, enables nearly lossless laser energy transfer through refractive optics, with a high flexibility of energy distribution in one plane or along the beam axis, for example between single laser spots, which has been shown to improve process quality.
Recently we've installed and tested Adloptica's QuattroXX and FoXXus refractive optics in the laser laboratory at Luleå University to explore the effects of beam shaping on laser material processing at high power. Both optics are capable of splitting a laser beam into up to four separate beams. The QuattroXX produces spots beside each other, while the FoXXus enables manipulation of the beam waist distribution along the beam axis (see figure 1). For both optics, the distance between the spots is defined by the optical setup, while the intensity in each spot can be manually changed by rotating the optical elements relative to each other.
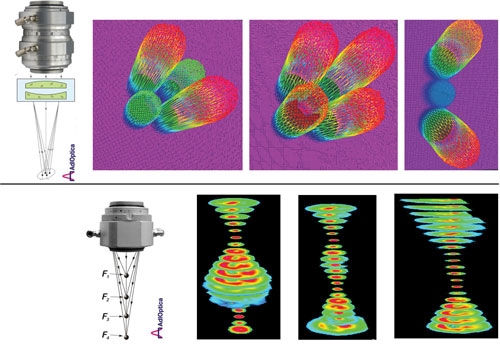
Figure 1: Optics and beam measurements of up to four beams next to each other (top, QuattroXX) and along the beam axis (bottom, FoXXus)
Bridging the gap
A widely known challenge in laser welding is gap bridgeability. Due to its typically small dimensions, a high intensity laser beam can transmit through the gap between the joining partners. This leads to a loss of energy and a reduced energy input for the welding process, which can be interrupted or lead to a reduced penetration depth, lack of fusion and thereby reduced mechanical properties.
Using the beam shapes enabled by the QuattroXX, it was possible to increase the bridgeable gap width from 0.1 to > 0.4mm in the used setup. Two dual-phase steel sheets (DP800 and DP1000 at 1.1mm thickness) were joined in butt joint configuration at a laser power of 3kW (15kW IPG fibre laser) and a processing speed of 3m/min, welded in the focal position of the beam.
As the energy input can be shifted to the joining partners without gap transmission losses, the optic's additional feature of varying energy densities between individual laser spots also opens up new possibilities in joining dissimilar materials by tailoring the beam to their boundary conditions. Such as by applying a higher energy input into the material with a higher melting point.
These first tests using the same processing parameters, as described above, indicate that tailoring the heat input even improves the joining of sheets with different thicknesses by guiding the melt and enabling robust bonding. This effect was shown for a DP800 (2mm thickness) and a DP1000 (1.1mm thickness) configuration, while the focal position of the laser beam was positioned on the material surface of the DP800 sheet. In addition, the distribution of laser energy into several spots next to each other was found to enable a reduction of spatter in the deep penetration welding of steel sheets. Spattering can occur when the metal vapour exiting from the vapour channel detaches melt drops from the surrounding melt pool. The wider opening of the vapour channel using multiple beams can lead to a decreased melt detachment probability, and therefore a higher quality weld seam and less solidified spatters attached on the welded parts.
The creation of up to four beam waists along the optical axis using the FoXXus optic denotes a quasi-elongated depth of field. The experimental setup consisted of a beam created by a 15kw IPG fibre laser, guided by a 100µm diameter fibre to create the several foci with a focusing lens of 200mm focal length. A laser power of 5kW at a processing speed of 7.5m/min, including argon gas shielding, was applied. Experimenting with both titanium and steel alloy sheets of 1mm thickness indicated the positioning of the laser beam waists influences spattering, while the created wider keyhole opening supports spatter suppression. It is assumed the more homogeneous energy input into the depth of the vapour channel leads to a more stable process (figure 2).
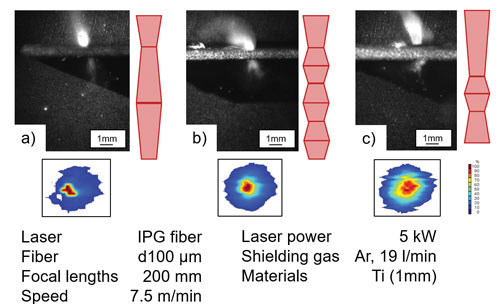
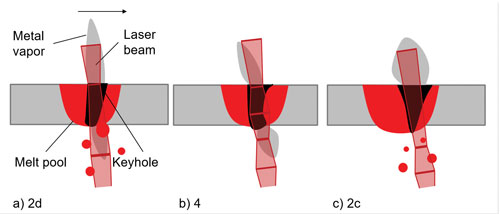
Figure 2: High-speed images (top) and vapour channel appearance (bottom) at different beam shapes produced with FoXXus with several beam waists along the optical axis: a) two distant beam waists, b) four beam waists and c) two close beam waists
An additional feature of the FoXXus laser beam is the creation of multiple different spatial intensity distributions along the beam axis. In the beam waists, the fibre end is visible as a tophat profile. However, the central tophat profile is superpositioned by the other beams, which leads to additional intensity around the central spot. Such beam intensity distributions are assumed to support welding, cladding and additive processes in the future.
Outlook
Refractive beam shaping offers the possibility to produce several tailored beam shapes at low cost. We have identified fields of applications for refractive beam shaping at high laser power, which offers a promising parameter for laser process optimisation. High potential applications are seen in additive manufacturing, to reduce process dynamics in powder bed processes or increase the process efficiency in directed energy deposition by tailoring the melt pool dimensions. Spatter reduction and increased gap bridgeability were achieved when welding steel and titanium sheets at high laser power. However, the findings indicate that the effects can be reproduced and transferred to further materials and process dimensions.
Laser light instead of finger pricks – how beam analysis paves the way to non-invasive blood glucose monitoring
More than 400 million people worldwide suffer from diabetes. For them, the ability to measure blood glucose levels non-invasively (without piercing the skin) would be an enormous relief. Thanks to a patented development by DiaMonTech AG, this dream could soon come true for many people. The company has developed the first non-invasive blood glucose meter, obtaining CE approval for the desktop version as a medical device in 2019. In order to miniaturise the technology without loss of quality, it is necessary to detect even minute changes in the laser beam. DiaMonTech uses the Ophir Pyrocam to measure and characterise all their lasers during development.
Deep innovation
The D-Base – as the desktop device is called – works based on infrared spectroscopy, and specifically by the principle of photothermal deflection. For this purpose, a quantum cascade laser radiates infrared pulses in wavelengths ranging between 8 and 11\'b5m onto the skin reaching epidermal layers. The light pulses of these wavelengths pass through the sensor element and excite the glucose molecules. Through the relaxation process a small amount of heat is released to the environment. At the skin surface this results in a periodic minimal increase in temperature. In the sensor element (internal reflection element \'96 IRE), the thermal gradient causes a thermal lens effect. The probe beam of a red laser diode is deflected by this thermal lens as it passes through the IRE. The deflection is measured by a position-sensitive photodiode; the device calculates the glucose concentration based on the deflection.
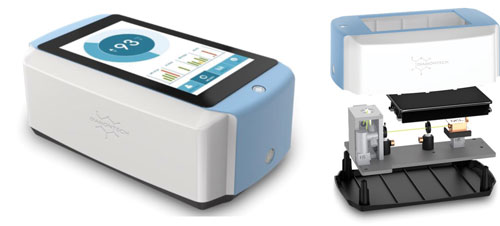
Figure 1: D-Base, the non-invasive blood glucose meter from DiaMonTech
Miniaturisation as a goal
The measuring principle has now been proven in everyday clinical practice, but shrinking the size of the measuring device is still a challenge. Sergius Janik, chief operating officer at DiaMonTech, explained: 'Diabetes patients want fast and compact measurement technology that they can easily use at home and on the road. This is the focus of our current research.' Only a few manufacturers offer the tunable quantum cascade lasers that DiaMonTech uses for the D-Base. In order to evaluate the quality of a given quantum cascade laser, the DiaMonTech lab staff conducts detailed measurements on all lasers to measure parameters, such as beam profile, output power, divergence, pulse repetition rate, pulse-to-pulse stability, shape of the pulse and focal spot on the skin.
After in-depth research and conducting an array of tests in their own laboratories, the experts decided on the Ophir Pyrocam-III-HR-C-A-PRO. Using this high-resolution pyroelectric matrix camera by MKS Instruments, the beam profile of an infrared laser can be measured both quickly and reliably. For the application at DiaMonTech, the camera was individually calibrated to the appropriate signal level. The camera data is then evaluated with the BeamGage software. Output power, beam profile and beam divergence can be determined by the camera in just a few seconds.
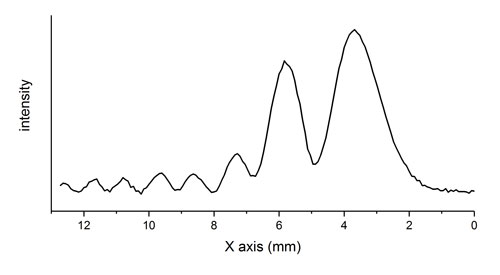
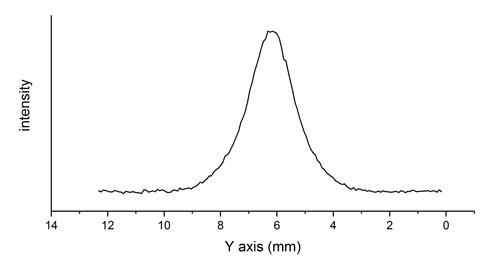
Figure 2: While the beam has the desired Gaussian distribution in the y-axis, the profile of the x-axis is very uneven
Troubleshooting made easy
Janik describes a concrete application as an example of the enormous time savings achieved by the Pyrocam. During a series of tests conducted by the DiaMonTech lab on a new laser, the engineers were unable to find the cause for a series of strange beam properties. The power distribution of the beam was very irregular, but the root cause was not obvious at first glance.
Only the images taken with the Pyrocam provided an explanation. Instead of the desired symmetrical Gaussian beam profile, the beam appeared strongly distorted (see figure 3).
These results showed that the collimating lens of the beam was out of adjustment, which may have occurred during shipment. The laser system was sent back to the manufacturer, the lens was re-adjusted, and after repair the Pyrocam measurements showed a uniform beam profile, as in figure 3 (bottom image).
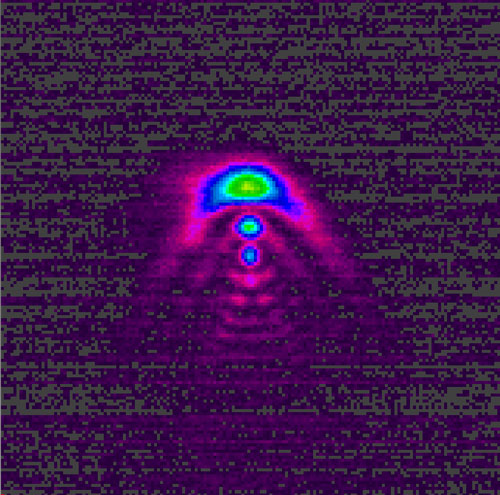
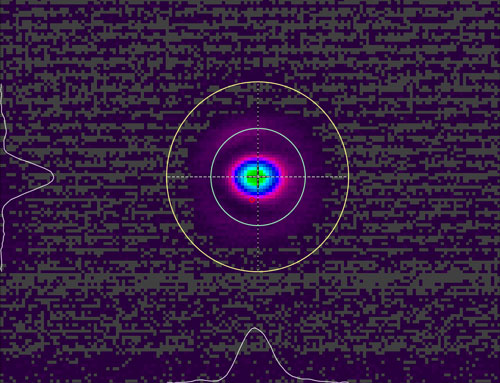
Figure 3: Imaging of the original beam profile using the Pyrocam: the top image is before lens adjustment, the bottom image is after
Faster measurements mean more efficient development
Along the road to miniaturisation in non-invasive blood glucose monitoring, there is no way around a camera-based measurement of laser beam profiles. Janik appreciates the measurement technology: 'The Pyrocam makes our daily work easier. We no longer waste hours on time-consuming measurements; rather, we get reliable results very quickly. This allows us to concentrate on the essential parts of development.'
Ophir Spiricon Europe
(MKS Instruments)
Guerickeweg 7
D-64291 Darmstadt
+49 6151-708-0