Generally known as optics of more than 0.5m in diameter, large scale optics such as lenses and mirrors are frequently used in telescopes for astronomy programmes, as well as in high power laser facilities. Today, they are being more frequently investigated in terms of transferring these properties for use in newer applications such as inertial fusion driven by high-power lasers.
Emerging technological developments, such as advances in petawatt laser technology, have also been instrumental in producing the latest generation of large optics, thanks to their ability to develop large surface area dielectrically coated mirrors to guide even demanding ultrashort pulse laser beams.
Coatings are crucial for all optics, and here particularly large optics to help enhance performance, durability, and efficiency. They can help to control light reflection, transmission, and absorption, ensuring that optics can handle intense laser pulses without damage. Coatings also need to improve the laser-induced damage threshold (LIDT), maintain uniform optical quality over large areas, and provide lowest absorption to reach highest reflection values and minimise thermal effects. Additionally, well calculated layer stacks, so called chirped mirrors, can manipulate the phase of the light which is important for numerous ultra fast laser applications.
The importance and complexity of optical coatings
Anyone developing or working with lasers, from scientific or technical backgrounds, and engineers in fields such as material processing and fundamental research areas at universities fully understand the importance and the complexity of optical coatings. Dr. Thomas Willemsen, Team Lead Coating Design at LASEROPTIK, a manufacturer of high-power optics and coatings which is, this year, celebrating its 40th anniversary, says: "The understanding of thin films has been its own research field for many decades and requires deep knowledge in physics and mechanical engineering. Each laser configuration can be different and requires a well-adapted set of parameters for manufacturing special optical coatings." This complexity necessitates collaboration with professionals in the field of optical coatings to ensure that the right optical components are used for the success of the individual laser application.
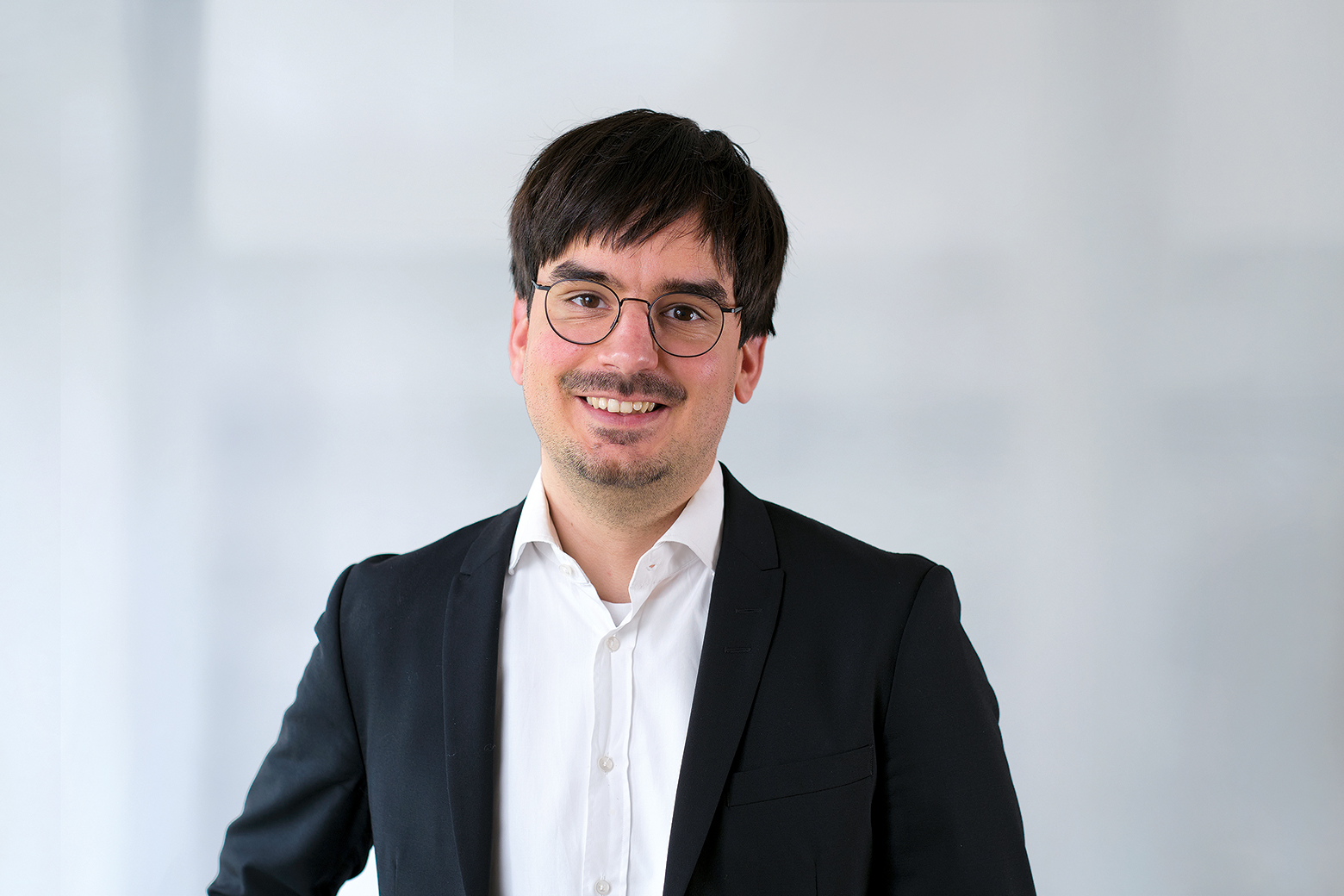
Dr. Thomas Willemsen, Team Lead Coating Design at LASEROPTIK GmbH, Horster Str. 20, 30826 Garbsen, Germany (Credit: LASEROPTIK)
One of the particular challenges in coating large optics is achieving a uniform coating across a large surface area. Says Willemsen: “The main challenge is to adapt the coating process for large-sized optics. For instance, achieving a homogeneous coating on substrates with >550mm (either diameter of round shaped blanks or diagonal of rectangular substrates) or more requires the development of enhanced target rotation systems and the control of process parameters.”
Ion beam sputtering (IBS) is one of the most precise coating techniques used to manufacture optical components. Thereby an ion beam is focused on a target material, which again sputters atoms from the target. In combination with a reactive gas like oxygen a well defined dielectric thin film deposited on e.g. rotating glass substrates above the target assembly. This process ensures high uniformity and density of the coating, which is crucial for the performance and durability of optical components used in high-power laser systems, such as petawatt lasers.
Improved laser-induced damage threshold
Willemsen explains: “For ultra-short pulse lasers, the damage mechanism is driven by the electronic states of the coating material itself. You can improve the laser-induced damage threshold by manipulating e.g. the electric field inside the layer stack." This precise manipulation is achievable with the IBS process due to its ability to maintain sub-nanometer precision over coating thickness, which is essential for developing complex coating designs.
In terms of the advantages of IBS, Willemsen highlights physical properties of sputtered layers and reliability and reproducibility of the IBS process, saying: “The main advantage comes from the coating structure itself. Conventional evaporated coatings are more porous, but IBS coatings are very dense and hard." This density and hardness provide possibility to do ultrasonic cleaning of sputtered optics and most important sputtered layer stacks are independent of the surrounding media. This means that sputtered components show, for example, no spectral shift when humidity increases or when optics are operated under vacuum.
IBS achieves lower optical losses
Another advantage is the ability of IBS to produce coatings with lower optical losses and often higher damage thresholds, which are critical for applications requiring high-power laser performance. Willemsen explains that this is particularly important for large laser facilities, where "the lifetime of the optics needs to be very good because when you need to change the optics after a few laser shots, it leads to longer downtimes and limits economic efficiency."
One challenge involved with IBS is achieving a homogeneous coating over larger areas. Willemsen explains "Homogeneous deposition over a large area is not as easily achieved as with evaporated coatings." To overcome this, LASEROPTIK developed a dedicated target rotation system and enlarged its sputtering equipment to ensure uniform coatings on larger substrates up to 550mm in diameter and a maximum substrate weight of 50kg. To further improve the LIDT, the company focuses on the manipulation of the electric field within the coating material, using complex coating designs. By addressing these challenges, LASEROPTIK ensures that its IBS-coated optics can meet the highest standards of quality and performance for advanced laser applications.
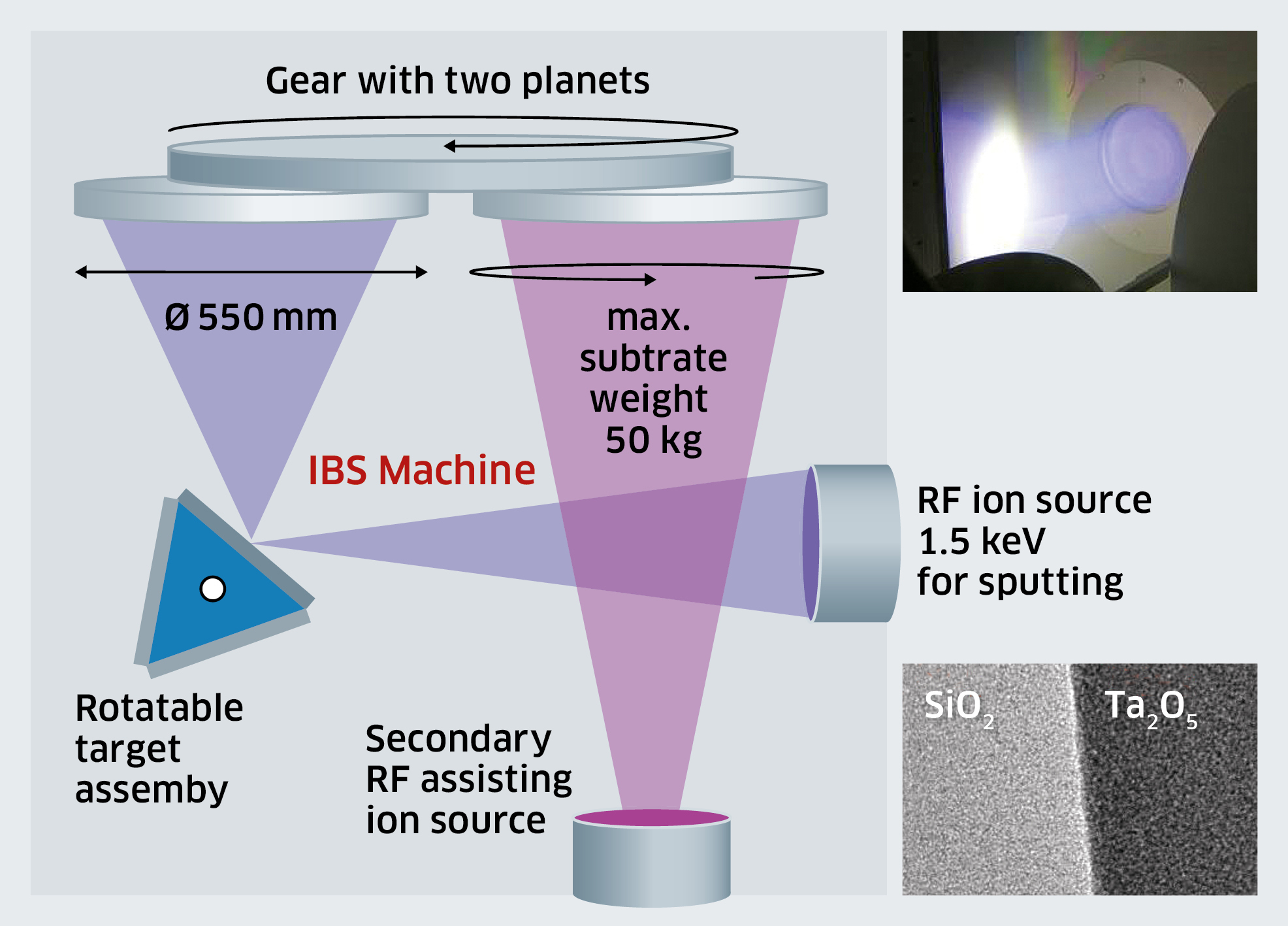
Two substrates up to a diameter of 550mm and maximum weight of 50kg can be deposited. IBS-technology enables reliable deposition of most complex designs (Credit: LASEROPTIK)
IBS coating techniques: Future applications
Looking to the future, Willemsen sees significant need in improved optical coatings with a laser induced damage threshold beyond state of the art. He says: "Simply spoken, a laser beamline can be just as powerful as the optical components allow." The primary future challenge, according to Willemsen, is "to achieve a reliable coating process so that large sized objects can be reproduced, reliable, and have the same losses and the same good quality around the huge area as the small substrates."
In particular, Willemsen highlights laser driven inertial fusion as a key area, which require the need for advancements in material science to "further improve the laser-induced damage threshold," and the importance of government-funded projects to accelerate development. He says: "Governments are spending millions of dollars for projects to achieve inertial fusion for the commercial generation of power. First breakthrough inertial laser fusion experiments were done successfully at Lawrence Livermore National Laboratory (LLNL) in the U.S. in December 2022. "
Specifically, he refers to the latest German research project called PriFUSIO (Federal Ministry of Education and Research (BMBF) within the “Fachprogramm Fusion 2040 – Forschung auf dem Weg zum Fusionskraftwerk” under contract no. 13F1000I), which was announced in April. The consortium of seven industrial partners and three research institutes is setting out to research key photonic components for laser-based fusion and make them usable in industry. The German Federal Ministry of Education and Research has awarded €18m for the project over the next three years. LASEROPTIK was selected to bring in its knowledge for the development of new optical large sized mirrors within the frame of the project PriFUSIO.
Says Willemsen: “LASEROPTIK was selected as a coating company. As a first milestone laser damage set-ups need to be developed which are capable of testing with large beam sizes. This is done by Laser Zentrum Hannover. When you're testing the laser-induced damage threshold right now, there are test setups available where you can test with a laser diameter of maybe 300 microns, but the laser damage threshold behaves totally differently for larger beam sizes." The ultimate goal, Willemsen explains, is "to build a laser for laser-driven inertial fusion power plants, with dielectric large sized optics which ensure a stable and 24/7 laser operation mode. Down times of the complete power plant due to damaged optics have to be avoided. The upscaled deposition process IBS for such needed regular sized optics is most promising to provide the commercial inertial fusion power plants."
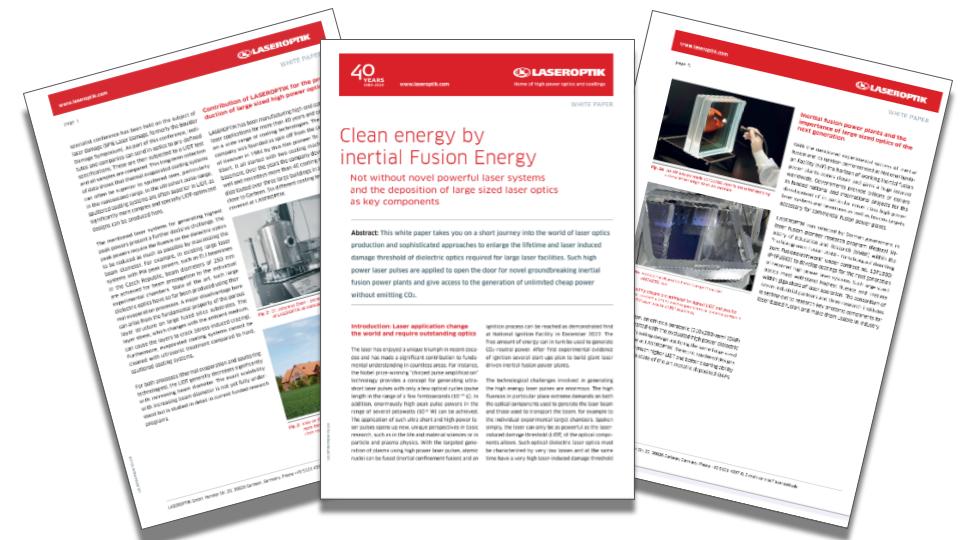