The automotive industry is constantly evolving, and with new developments in light sources comes a number of trends that are changing the look and feel of vehicles. From narrow bands of light to homogeneous luminous surfaces, automakers have a range of styling options available to give their vehicles an elegant and sophisticated aesthetic. In this article, we will look at one optical technology for realising such trends in automotive lighting technology, free-form micro-optics.
Current standard: free-form macro-optics in automotive lighting systems
Classic free-form optics, which can certainly be called free-form macro-optics, have been used in automotive lighting for many years. In addition to free-form reflectors, typical applications are TIR optics and imaging optics in headlamp systems. Figure 1 (below) shows examples of these types of optics. The freedom of the design of optically active surfaces is particularly attractive for the light shaping in headlamp applications. In addition, coupling-in and coupling-out optics for light guides in tail lights and signal lights are designed as free-form optics and, like TIR optics, offer the advantage of increasing the efficiency of the system.
Figure 1: Free-form macro-optics in automotive lighting
Regardless of the field of application or the specific shape of the optics, the free-form macro-optics have the advantage that they can be manufactured with typical process standards in the field of automotive optics manufacturing, injection molding.
But in contrast to these advantages, the free-form macro-optics have the decisive disadvantage that they are macro. In terms of styling, this means that the optical elements themselves, but also possible free-form macro-structures on surfaces, are visible to the observer even from a greater distance. This circumstance is no longer compatible with current styling trends, which focus on the visual integration of optical systems into the vehicle body or completely hiding such systems.
This is the point where micro-optics come into play. They not only offer the possibility of reducing the dimensions of the optics – if desired – but in particular of optimising the optically effective surfaces with regard to the visibility of curvatures or structures.
The free-form micro-optics thus combine the design freedom of free-form optics and the advantages of micro-optics. The resulting potential for various fields of application, including automotive, is enormous.
Potential fields of application for free-form micro-optics in automotive applications
With regards to the mentioned styling trends in automotive lighting, a top field of application for free-form micro-optics is their use as diffuser optics to create homogeneous luminous surfaces. In recent years, HELLA has presented the FlatLight family of different technologies for the realisation of such luminous surfaces with particularly low installation space.
Figure 2: HELLA's FlatLight technology is an example for the potentials and benefits of free-form micro-optics
The FlatLight family includes the FlatLight|μDO (μDO stands for microdiffuser optics) and the FlatLight|μMX (μMX refers to the optical microstructures generating a maximum photometric output) variants, which use free-form micro-optics to direct and distribute light.
The FlatlLight|µDO is a light guide with a surface completely covered with microstructures in order to create a large, homogeneous luminous area. Therefore, microstructures with sizes smaller than 100 μm are used and manufactured with lithographic processes.
The FlatLight|µMX is a bit more complex. This variant consists of a light guide with multiple optical layers. These optical layers use different freeform micro-optics and diffuser optics to realise an impressive homogeneity in combination with a great efficiency.
The FlatLight technology is just one example for the potentials and benefits of free-form micro-optics. There are many other applications in which free-form micro-optics can enable new developments:
-
Optics for sensors
-
Displays / HUDs
-
Beam shaping optics
-
Compensation of colour aberration
-
Projection optics
Looking at this list of applications, one or the other reader might wonder why free-form micro-optics are not already widely used in automobiles. This is due to the various requirements placed on optical components in the automotive environment.
-
High optical surface quality esp. for imaging optics with low roughness (<40nm, better <10nm)
-
Cost effective mastering and series production comparable to injection moulding
-
Usage of automotive certified materials that withstand automotive environmental conditions
-
2D, 2.5D and 3D curved substrates to enable visual integration of optic into the car body.
-
fabrication of large-scale optics, e.g., tail or car body lamps
-
Data handling of large-scale optics to simulate the entire lamp system, e.g., for stray light analysis
-
Interface for design and simulation tools to avoid data errors due to long tool chains
This list of challenges is a broad overview of the requirements from different applications and not all requirements have to be fulfilled for every application, but a combination of at least 4 of the mentioned points is always to be expected when integrating free-form micro-optics into an automotive lighting system.
Now, one or the other reader will certainly think that this should not be a problem, after all, there are enough capable companies out there that have already specialised themselves to one or the other topic. But mostly the challenge remains to find these companies and to link their competences to a process chain that works for series production. A big effort, which cannot be organised by every company. This is where the PHABULOµS pilot-line comes into play.
PHABULOµS Pilot Line
PHABULOµS is an EU-funded project that aims to set up a European pilot line for the manufacturing of free-form micro-optical components by UV replication technologies (wafer-scale, roll-to-plate R2P, and roll-to-roll R2R) with a clear roadmap for high volume production at competitive cost.
Since the start of this project in January 2020 HELLA is one of the use-case partners and works together with the pilot-line partners on the development of a new optical system for headlamp applications - of cause including freeform-micro-optics.
In order to exploit the advantages of free-form micro-optics, HELLA is pursuing the target of combining primary and secondary lenses and shutters in one micro-optical component. At the same time, the process of the pilot-line is being tested from design to replicated components.
Let’s have a look at the current results.
The idea of the HELLA design is to use the light input side of the component as primary optics and the light output side as secondary optics to shape the light distribution. Both high and low beam distributions were investigated with different optical structures as part of the project. In initial testing, a micro-Fresnel lens was used on the first surface and a free-form facet structure was used on the second surface. Figure 3 shows an example of a facet structure for generating a low beam distribution.
Figure 3: example of a first state free-form micro-optic with a facet structure to generate a low beam distribution
For the first fabrication step, the mastering, different partners of the pilot-line analysed the structures with regard to their origination capabilities. The mastering of the facet structure was a challenging task due to the steep edges and the different orientations of the 300µm large facets in combination with the required surface quality. Here, the advantages of the PHABULOµS pilot-line network became apparent: the partners transparently discussed the manufacturing possibilities to find the best solution for the specific structure. If one partner found that the process did not fit, other partners were able to step in and support the pre- or post-processing or took over the entire mastering.
Finally, Wielandts UPMT took over the generation of the master of the Fresnel lens and PowerPhotonic the mastering of the free-form micro-structure. With their ultra-precision machining technique, Wielandts UPMT was able to produce an excellent shape and surface finish.
For the mastering of the facets structure, the process parameters and the design had to be precisely aligned to avoid stray light resulting from a smoothing of the structure. Together, HELLA and PowerPhotonic found a solution to keep the manufacturing effects at a minimum.
HELLA’s partners for the replication are SUSS MicroOptics and Nanocomp. A special aspect of the replication was the combination of the two masters into one component. Even though the Fresnel lens generates theoretically parallel light, a high precision in the alignment of the optical surfaces to each other is required to avoid scattered light on the one hand and a reduction of efficiency on the other hand.
Both SUSS MicroOptics and Nanocomp proved that their processes meet the requirements. Figure 4 shows a replica from Nanocomp. The total component is not larger than a one cent coin, and in the case of using the R2R process even thinner than this!
Figure 4: Example of a double-sided free-form micro-optic replicated by Nanocomp - as small as a one cent coin and even thinner
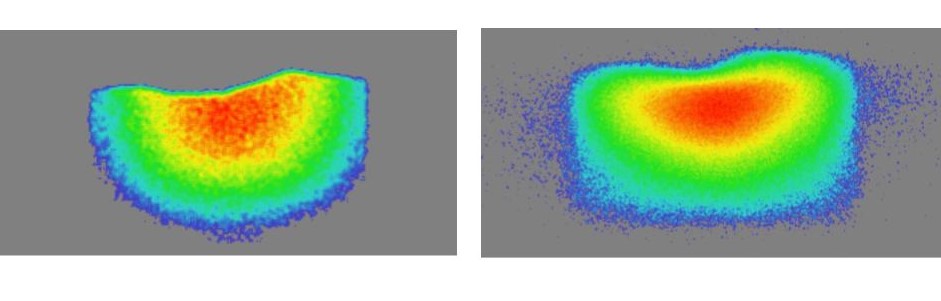
Conclusion
The use case HELLA has chosen for the PHABULOµS project is one of the most challenging in automotive lighting. It is expected that applications with less demanding requirements that do not need hard cut-offs could already be implemented with this technology.
And even if the headlamp use case in particular still needs further developments, the potentials proofed by simulations and the results HELLA already presented with their FlatLight technology should encourage everyone to deal with the topic of free-form micro-optics.
About the author
Daniela Karthaus works in the Innovations department at FORVIA HELLA and is an expert for lighting technology and optics. She evaluates new technologies for automotive lighting applications, has several years of experience in micro- and diffractive optics and did research on holography for her PhD. Since January 2020, she has coordinated HELLA’s activities in the PHABULOUS projects.