Additive manufacturing, commonly known as 3D printing, is reshaping industrial production. By building parts layer-by-layer directly from digital designs, this technology eliminates the need for traditional tooling, speeds up prototyping, and cuts production costs. Now, with photonic technologies playing an increasingly critical role, 3D printing is reaching new heights in precision, speed, and material versatility.
Key 3D printing techniques in industry
A range of 3D printing techniques are utilised in industrial manufacturing, each suited for specific materials and applications.
Stereolithography (SLA)
Stereolithography (SLA) uses a laser to solidify photosensitive resin layers, producing high-resolution prototypes. Ultraviolet (UV) LEDs have recently replaced lasers, offering greater efficiency.
Selective laser melting (SLM)
Selective laser melting (SLM) employs a laser to fuse metal or plastic powders, creating durable and complex parts. SLM is ideal for applications requiring high precision and strength, often used in the aerospace and medical sectors where safety and performance are critical.
Selective laser sintering (SLS)
Selective laser sintering (SLS) uses a laser to sinter plastic, metal, or ceramic powders into solid parts. Unlike SLM, which fully melts the material, SLS heats the powder to the point of fusion, making it ideal for functional prototypes and end-use parts that require durability.
Binder jetting
Binder jetting works by spraying a binding agent onto layers of powder material to create solid objects. This method is particularly effective for producing large, complex parts, when intricate geometries are required.
Directed energy deposition (DED)
Directed energy deposition (DED) utilises focused energy sources, such as lasers, to melt and fuse material as it is deposited onto a substrate. DED is often used to repair existing parts or add material to create complex structures.
Laser-assisted fused deposition modeling (FDM)
Laser-assisted fused deposition modeling (FDM) combines traditional FDM printing with lasers to improve precision and material bonding during printing. This method is often used for prototyping and small batch production and allows a wider range of materials to be used, including specialised composites.
The role of photonics in evolving 3D printing capabilities
Photonics is advancing 3D printing by enabling ultra-precise, high-speed manufacturing. Light-based techniques like two-photon polymerisation, upconversion nanoparticles, and multi-photon lithography allow printing of complex structures at resolutions down to 100 nanometers, expanding the capabilities of additive manufacturing.
Key photonic tools from Hamamatsu Photonics transforming 3D printing include:
Spatial light modulators: LCOS-SLM
LCOS Spatial Light Modulators (SLMs) from Hamamatsu Photonics are known for their high laser damage threshold. As a result, LCOS-SLMs can split a powerful laser beam into multiple beams, each of which is capable of simultaneous 3D printing. This capability not only improves throughput but also allows better printing quality while using less number of lasers. The result is the creation of complex metal parts without tooling or molds, reducing lead times, material waste, and assembly steps—while maintaining mechanical performance comparable to traditional methods.
Benefits of Hamamatsu’s LCOS-SLM X15213 series:
- Wide wavelengths: 400 to 2050nm
- Laser power handling up to 750 W (in the spectral window 1000-1100nm)
- High light utilisation efficiency
- High-precision, high-linearity modulation characteristics for a specific wavelength
- High diffraction efficiency
UV-LED light sources
Compact and powerful UV LEDs (280–405nm) deliver precise resin curing for consistent layer solidification. Dual-wavelength output (365 nm & 280 nm) enhances curing efficiency and material performance.
Benefits of Hamamatsu’s UV-LED technology:
- Excellent 3D printing quality
- Guaranteed structural integrity of the part
- Reduced heat generation
Semiconductor lasers: SPOLD®
Compact, fibre-coupled lasers with customisable beam profiles for targeted energy delivery. Ideal for 3D printing and related processes like polymer welding and metallic ink sintering.
Benefits of Hamamatsu’s SPOLD:
- Wide power range from 9W to 360W with several wavelengths
- 'Top hat beam profile' for uniform intensity distribution
- Compact, customisable, easy to operate and equipped with in-built temperature monitoring
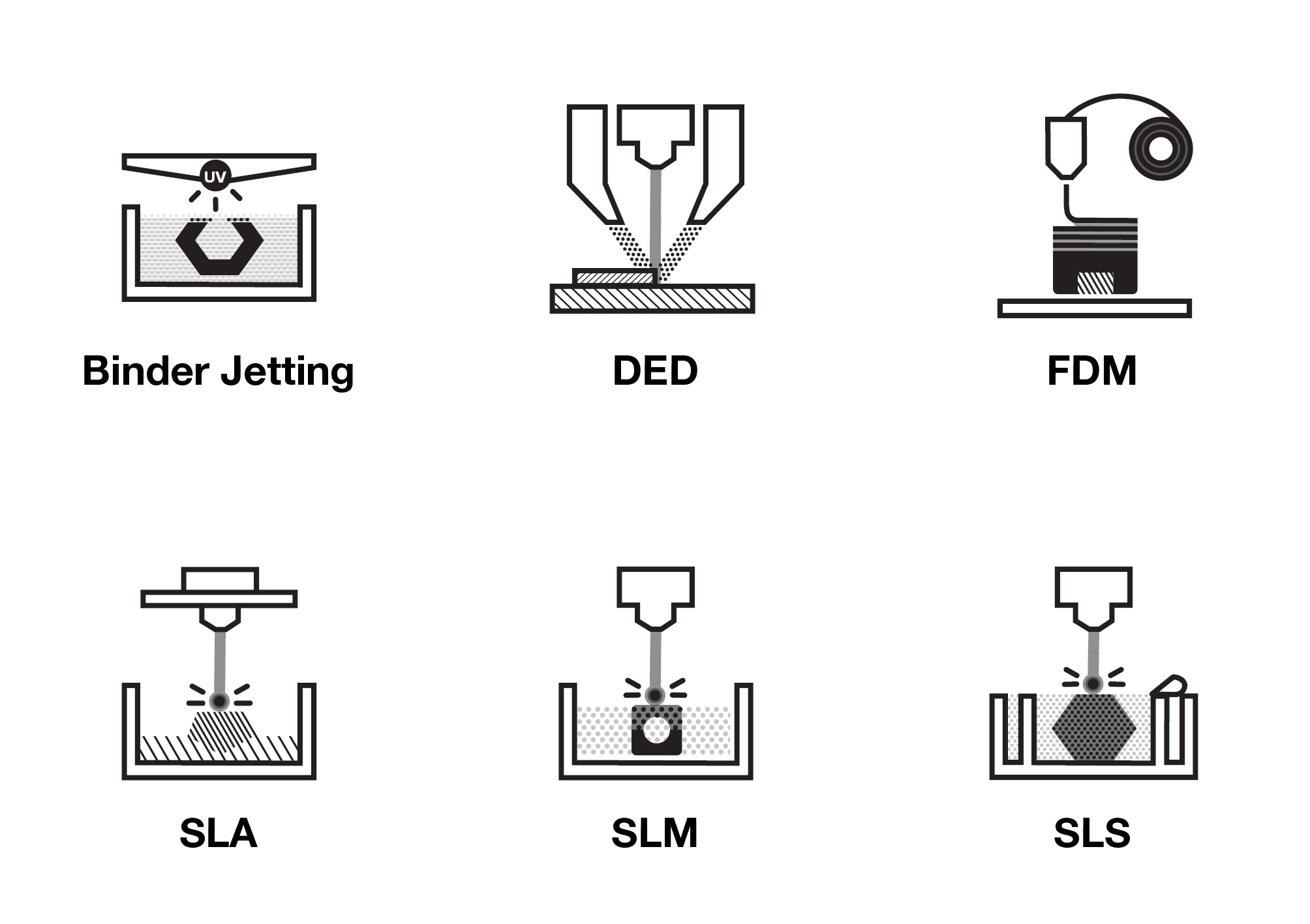
3D printing is reshaping industrial production (Credit: Hamamatsu)
NIR semiconductor lasers offer promising developments in 3D printing. In addition to the benefits stated above, they can initiate cross-linking directly at the focal point, showcasing the potential for low-cost direct laser writing in volume and 3D printing. NIR lasers can also be integrated into ink-based 3D printing technologies to solidify filaments with diameters up to 4mm, surpassing the limitations of UV-based curing in terms of range and intensity.
Conclusion: The future of 3D printing in industrial equipment
3D printing has the potential to significantly transform industrial manufacturing. This technology enables the creation of innovative designs, minimises waste, and enhances efficiency. With the ongoing advancements in materials and technology, combined with the essential contributions of Hamamatsu Photonics in enhancing the precision and quality of 3D printing, the future of industrial equipment manufacturing looks promising and tailored to meet specific needs.
References
Q. Zhang, A. Boniface, V. K. Parashar, and C. Moser, "Multiphoton polymerization using upconversion nanoparticles for adaptive high-resolution 3D printing," vol. 12433, pp. 124330C-124330C, 2023, doi: 10.1117/12.2650323.
"Multi-photon polymerization using upconversion nanoparticles for tunable feature-size printing," 2022, doi: 10.48550/arxiv.2211.01437.
"Micro‐Optics 3D Printed via Multi‐Photon Laser Lithography (Advanced Optical Materials 1/2023)," Adv. Opt. Mater., vol. 11, no. 1, pp. 2370001-2370001, 2023, doi: 10.1002/adom.202370001.
Lovera, M. O. Giacone, C. G. E. Alfieri, E. Casamenti, and R. Ferrini, "3D printing of glass micro-devices for integrated photonics and miniaturized optics," 2023, doi: 10.1117/12.2649093.
Hamamatsu Photonics, "3D Printing," Hamamatsu Photonics.