The simplest, and most common, laser processing technique used for micromachining is percussion drilling. In this technique, laser light is focused to a small, round spot. The size of the feature that can be machined is determined by the size and shape of the focal spot, while the depth is determined by the pulse duration, power and number of pulses used. The percussion technique allows the drilling of many holes very quickly – typically hundreds of holes every second.
For some applications, however, percussion drilling does not provide the accuracy or shape of feature required. To achieve greater accuracy and shape flexibility, systems can be used that more precisely align the workpiece and laser beam. For example, very high precision circular holes (±0.2mm) can be drilled using an optical trepanning technique. More complicated shapes can be made using multi-axis machining systems, including galvanometer-scanning heads, which can effectively mill away the material. For larger parts, it becomes more appropriate to cut the material rather than to mill it away.
This method is particularly useful for machining components, such as fuel injectors for the automotive industry. The holes in fuel injectors must be extremely precise, as the size of the hole governs the flow rate of fuel into the cylinder of the engine. Any inaccuracies would result in incorrect fuelling, which in turn would lead to poor engine performance, reduced fuel economy, greater engine wear, and ultimately, shortened engine life. Laser drilling equipment, from companies such as Oxford Lasers, allows manufacturers of fuel injectors to produce nozzles with multiple angled holes – with smaller diameters than traditional methods. This gives vehicle engineers better control of the flow of fuel vapour within the engine, so they can extract as much energy from the fuel as possible, while reducing emissions.
When injection moulding plastic components, such as aerosol nozzles, traditional methods of creating small orifices in the components involve the manufacturer placing small pins in the mould. This method is limited as the pins eventually wear out or break and need to be replaced, resulting in production down time. A major drawback of this method is that it means that the manufacturer has to commit to a given orifice size and angle at the point of moulding the part. For volume products, like aerosol valves, where a single valve type may need to be produced with a range of sizes of orifices for different applications, this can be a significant disadvantage. By removing the requirement to create the hole in the moulding process, it is possible to produce blank components for stock and then laser-drill the required orifice in response to the customer's needs and demands. OpTek Systems produce laser micro-processing systems that are used for just this type of application, where customers demand high levels of precision, reliability of product specification, little wastage, and economy of production time in operation.
This type of so-called 'just-in-time' manufacturing reduces the number of parts and components manufacturers need to stock in their inventories by many millions of units. It also allows the manufacturer to respond rapidly to customer demands. Different or new hole sizes can be produced in the five minutes that it takes to programme the new size into the computer that controls the laser – there are no tooling delays.

This embolic filter acts as a net, trapping potentially dangerous debris during angioplasty procedures.
Five years ago, the medical micromaching market featured mainly stents and some fairly simple catheters. Today, the breadth of devices is staggering, encompassing stents, bioabsorbable or polymer stents, stent grafts, embolic filters, precision drug delivery devices, electrophysiology, neurological devices, many types of catheters, intravascular radiation delivery devices, angioplasty balloons, and femoral closures. Disposable medical devices are employed in an ever-growing number of minimally invasive procedures. The procedures for which these products are used typically result in lower overall treatment costs and shorter recovery times compared to traditional surgical approaches. Many of these devices are plastic-based products with unusual shapes and small dimensions.
The correct function of these products is critically dependent on their precise three-dimensional shape. This makes them ideally suited for production by UV laser micromachining, because it ablates plastic material in a cold process with almost no peripheral thermal damage or re-cast debris. Excimer lasers are often used for these applications, as they can deliver high pulse energy and high average power over a range of ultraviolet and deep ultraviolet wavelengths, at high pulse repetition rates, in the kilohertz range. This high pulse energy and average power translate into fast processing – always an important economic consideration for disposable products.
American firm Resonetics produces laser-machined medical devices; both high-volume generic components and more specialised, low-volume contract manufacturing. Many of its workstations are built around excimer lasers from Coherent, operating at a wavelength of 193nm or 248nm. These systems combine shaped (masked) beam profiles and the ability to move the workpiece in multiple axes to provide a high level of achievable detail.
Glenn Ogura, vice president of marketing at Resonetics, explains: 'Traditionally, plastic medical disposables were produced by moulding or by machining components with a mill or hot needle. However, these mechanical methods can no longer cope with the small dimensions of today's devices. Micromachining with lasers is a very versatile and flexible tool that can work at the micron level. For example, typical tasks for our systems include drilling through or blind holes, stripping insulation from wires or braided structures, and cutting intricate patterns.'
As well as machining parts directly, lasers are also used for producing moulds for plastic components and dies for metal pieces. Such moulds and dies are often used for manufacturing high volume, low cost components, such as razors, electrical connectors and even toy trains.
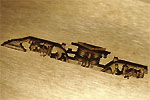
All aboard... a mould for a toy train created by Sauer Lasertec's equipment.
Lasertec – a company recently acquired by the Sauer division of Gildemeister – pioneered a laser micromachining technique called 3D ablation to create these moulds using a diode-pumped solid state laser with near infrared (1.06µm) output. The workstation can control and vary the delivery of the laser beam in three dimensions, including inclination of the laser attack angle. This allows shapes like spheres and cavities to be created, which would not be possible with conventional laser configurations with a fixed-angle beam.
Martin Reisacher is Sauer Lasertec's chief technical officer. He explains: 'Our system is designed to handle parts with overall dimensions as large as 300 x 200mm, but our customers often use these systems to make moulds smaller than 10mm. In all cases, the main considerations are precision and surface quality. The speed with which the moulds are created is much less important, because these moulds are high value components used over and over again to create many units of the final product itself. So even small defects and surface irregularities cannot be tolerated, as they would be reproduced in every one of the products that had been moulded.'
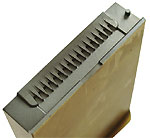
A die for a component of an electric razor, created using precise 3D laser ablation.
The trick to achieving high dimensional accuracy and a finish of good quality to the surface of the mould is to remove only a tiny thickness of material with each laser pulse. This requires a laser with high pulse-to-pulse stability. Initially, Lasertec used a lamp-pumped laser. Typical of lamp-pumped lasers this delivered high power, but with a multimode beam. Parts were produced quickly, but the surface quality and edge precision was not satisfactory. The company then switched to a diode-pumped Prisma laser from Coherent. Prisma is a modular laser platform that can be configured for a broad range of output characteristics. Lasertec uses a 15W version with the pulse duration, pulse energy and repetition rate optimised by Coherent to maximise surface quality in the moulds produced, regardless of processing time. With a laser spot size between 30 and 40µm, the material removal rate is around 0.1 mm3/minute. At this controlled ablation rate, the laser process results in a high-quality mould created over several hours.
As the demand for miniaturised products becomes greater, then laser-processing techniques, which allow features to be produced that could never be made using traditional methods, will become ever more prevalent in the micro-manufacturing industry.